
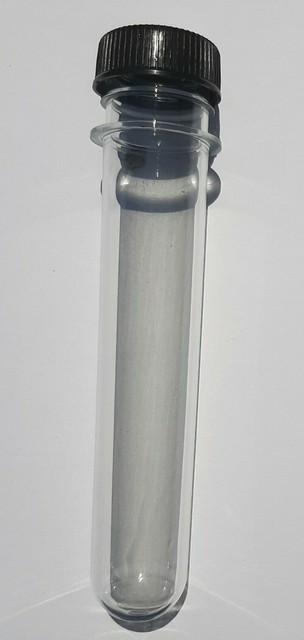
Examples are ethylene vinyl alcohol (EVOH), nylons, and polyvinylidene chloride (PVDC). These are plastics with a particular resistance to the transmission of water vapor or gases such as oxygen or carbon dioxide.

The construction usually includes one or more barrier layers. Increasingly, a mid layer may consist of recycled material which is encapsulated between inner and outer layers of virgin plastics.īMs commonly include from two to seven layers, although more are also used. The parison or preform is coextruded with a number of different layers, each of which contributes an important property to the finished product. Coextrusion and coinjection (or multilayer processes) are essential technique in the production of high performance BM products ( Chapters 4 and 5). 225, 226, 227 Care must be taken to control the process so that the melt when blown will not have micro-voids in the container walls or will delaminate. Technologies, such as coextrusion and coinjection, allow PET and other plastics to package foods and other products. Automotive and marine fluid bottles are molded of PVC because it provides hydrocarbon resistance and barrier properties that are not possible with untreated HDPE.

PVC is losing popularity but is still used in industrial packaging. If PET can be price-competitive with HDPE, then it is likely that PET will capture market share from HDPE bottles. Growth for PET in food and beverage containers will average 9% to 10%/yr over the next five years, but growth is expected to be only 2% annually for PET industrial BM containers due to HDPE's lower price and greater chemical resistance. PETs high clarity imparts greater shelf appeal. PET is also being utilized more frequently in containers. PET plastic in addition to being used in beverage bottles has started to appear in bottles for motor oil and other auto and marine fluids. HDPE accounts for nearly 90wt% of the plastic used. 215 216 217īM is the third largest plastic processing technique worldwide used for producing many different products. BM permits potential of consolidation of parts competing with other processes such as injection molding ( Chapter 4).Īpplications for BMs are used to contain many different products that include foodstuffs, beverages, household products (appliances, air conditioners, furniture at home/office/hospital/sports arenas, etc.), personal care products, medicine/pharmaceutical products, automotive parts, construction panels, tote boxes, trays, leisure items (toys, floatation, marine buoys, canoes, sailboards, sports goods, etc.), industrial parts (business machines, tool boxes, trash containers, hot water tanks, etc.), and so on. Virtually most products require no finishing or secondary operations. The surfaces of the moldings are smooth and bright, or as grained and engraved as the surfaces of the mold cavity in which they are processed. The process is to inflate a softened TP hollow form against the cooled surface of a closed cool female mold cavity where the plastic solidifies into a hollow product. Examples of extrusion, injection, and stretch blow molding techniques
